From fusion research into medical technology
Special materials developed from tungsten for fusion experiments – applicable in X-ray tubes?
Are other applications possible for the special heavy-duty materials developed from tungsten for fusion device components? Yes, says Mathias Sommerer, who tackled this question in a PhD thesis funded by Siemens AG, which he did at the Technical University of Munich. The information needed from fusion research was acquired from the material specialists at Max Planck Institute for Plasma Physics (IPP) in Garching.
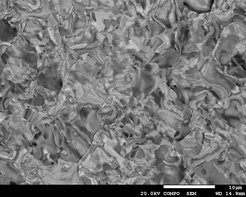
For his thesis Mathias Sommerer searched at IPP for results from fusion research that might be useful for industrial application. He got what he wanted from scientists investigating the interaction of the hot fusion plasma with the walls of the enclosing vessel. For this purpose they are developing materials capable of withstanding high loads.
The aim of fusion research is to reproduce on earth the energy generation of the sun. A fusion power plant is to derive power from fusion of atomic nuclei. Because the fusion fire does not ignite till a temperature exceeding 100 million degrees is attained, the low-density hydrogen plasma fuel ought not to come into contact with the cold walls. Confined by magnetic fields, it levitates inside a vacuum chamber almost without contacting it. Only at exactly defined locations – in the so-called divertor – does the plasma have wall contact. Tungsten, the metal with the highest melting point, has proved its worth for these highly loaded components. This has been demonstrated in extensive investigation at IPP. These have also taken care of a shortcoming of the otherwise very sturdy material: tungsten is brittle and therefore difficult to process; stress can cause cracking and the material may become fragile.
Fusion research has come up with possible remedies for this. The properties of the materials can be greatly improved with alloy additives or special microstructuring of the materials, various versions of which are being investigated at IPP and elsewhere. Mathias Sommerer thinks that this is just what might be of interest for other applications, e.g. for the anodes in X-ray devices, which are likewise made from tungsten-based materials: “The pulsed heat load that X-ray anodes have to withstand is roughly equivalent to the alternating load to which divertor plates are subjected in fusion devices in the case of certain plasma instabilities.”
The tungsten versions alloyed with rhenium hitherto used in industry are comparatively expensive. Mathias Sommerer therefore followed suit after IPP by trying out pure but particularly fine-grained tungsten structures: When loaded, the fine-grained microstructure involves shorter cracks that also do not propagate so readily because they are restrained at the many grain boundaries.
The production methods developed for fusion device components, e.g. powder injection moulding being investigated at Karlsruhe Institute of Technology, are, however, unfavourable for the larger and flat components needed by industry. Mathias Sommerer therefore adopted a new process, viz. tape casting: A slick of pulverised tungsten and organic binding substances is poured onto a moving conveyor belt. Subsequent heating to about 1,800 degrees sinters the soft material together to form a solid tungsten sheet. The scanning electron microscope at IPP then showed the fine-grained structure required.
All of this work was academically supervised at the Technical University of Munich by Prof. Dr. Ewald Werner, Chair of Materials Technology and Mechanics in the Faculty of Mechanical Engineering, which is linked with IPP through a joint professorship. The funding was through Siemens AG, whose Siemens Healthcare section ranks with Europes’s great suppliers of X-ray equipment. The process, for which a patent is pending, is now being tested at Siemens’s Erlangen laboratory. This involves bombarding the samples with an electron beam, just like what the anode is subjected to in an X-ray device. The more favourable fracture behaviour expected was in fact demonstrated. “We now want to find out”, states Siemens developer Dr. Steffen Walter, “whether the samples produced with the new method and used in real applications go beyond the present state of the art.” For example, it is being investigated whether longer lifetimes than hitherto are attainable. “Although tape casting can still be improved”, says Mathias Sommerer, “it is already clear that know-how from fusion research can advance the development of industrial applications, and that it is worthwhile to look for synergies.”
Isabella Milch